Recognizing Porosity in Welding: Discovering Causes, Effects, and Prevention Strategies
As specialists in the welding industry are well conscious, understanding the causes, effects, and prevention techniques associated to porosity is important for accomplishing durable and reputable welds. By delving into the origin creates of porosity, analyzing its damaging effects on weld top quality, and discovering reliable prevention strategies, welders can enhance their expertise and skills to generate high-quality welds consistently.
Usual Root Causes Of Porosity
Contamination, in the kind of dirt, grease, or rust on the welding surface area, creates gas pockets when heated, leading to porosity in the weld. Inappropriate shielding takes place when the shielding gas, generally made use of in procedures like MIG and TIG welding, is unable to totally shield the liquified weld swimming pool from reacting with the surrounding air, resulting in gas entrapment and subsequent porosity. Additionally, inadequate gas coverage, frequently due to inaccurate circulation rates or nozzle positioning, can leave parts of the weld unsafe, allowing porosity to develop.
Impacts on Weld Top Quality
The visibility of porosity in a weld can substantially endanger the overall quality and honesty of the bonded joint. Porosity within a weld produces gaps or tooth cavities that weaken the framework, making it a lot more at risk to splitting, corrosion, and mechanical failure.
Furthermore, porosity can impede the effectiveness of non-destructive testing (NDT) strategies, making it testing to find various other flaws or interruptions within the weld. This can bring about substantial safety and security concerns, especially in important applications where the structural integrity of the bonded parts is vital.
Avoidance Techniques Review
Given the harmful impact of porosity on weld high quality, effective avoidance methods are vital to maintaining the structural integrity of welded joints. Furthermore, selecting the appropriate welding criteria, such as voltage, current, and travel rate, can help decrease the risk of porosity development. By including these avoidance strategies into welding practices, the event of porosity can be substantially decreased, leading to more powerful and a lot more reputable welded joints.
Relevance of Appropriate Protecting
Appropriate securing in welding plays an important role in protecting against atmospheric contamination and ensuring the stability of welded joints. Protecting gases, such as argon, helium, or a mixture of both, are frequently used to secure the weld swimming pool from reacting with components in the air like oxygen and nitrogen. When these responsive elements enter contact with the hot weld swimming pool, they can cause porosity, bring about weak welds with minimized mechanical properties.

Inadequate shielding can result in various defects like porosity, spatter, and oxidation, compromising special info the architectural integrity of the bonded joint. As a result, sticking to appropriate protecting methods is important to create top notch welds with very little problems and guarantee the longevity and reliability of the bonded elements (What is Porosity).
Surveillance and Control Techniques
How can welders properly keep an eye on visit this web-site and manage the welding process to ensure optimum outcomes and avoid defects like porosity? One trick technique is via making use of advanced surveillance technologies. These can consist of real-time monitoring systems that give comments on parameters such as voltage, present, travel speed, and gas circulation rates. By continually keeping an eye on these variables, welders can identify inconsistencies from the optimal problems and make immediate changes to avoid porosity development.

Additionally, executing appropriate training programs for welders is necessary for monitoring and controlling the welding process efficiently. What is Porosity. Informing welders on the value of keeping regular criteria, such as correct gas securing and travel speed, can aid prevent porosity problems. Routine evaluations and qualifications can likewise make sure that welders are proficient in monitoring and controlling welding processes
In addition, making use of automated welding systems can boost surveillance and control capacities. These systems can exactly control welding specifications, decreasing the likelihood of human error and making certain regular link weld top quality. By integrating sophisticated monitoring modern technologies, training programs, and automated systems, welders can properly keep an eye on and manage the welding process to minimize porosity issues and accomplish premium welds.
Conclusion
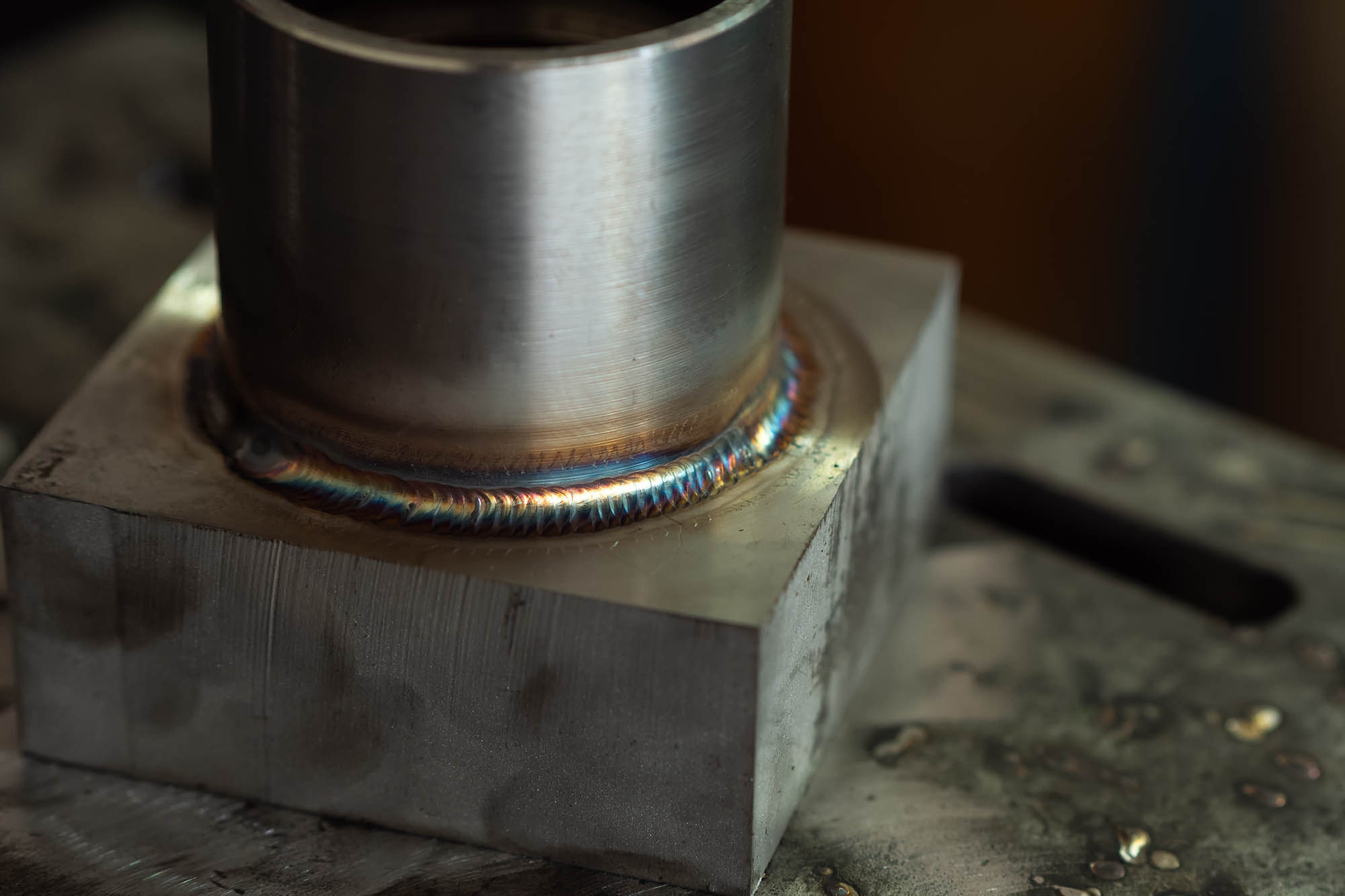
Comments on “What is Porosity in Welding: Comprehending Its Causes and Enhancing Your Skills”